Insight
What Automation Means for Your Real Estate Strategy
September 26, 2017 | BY Suzanne Grimm
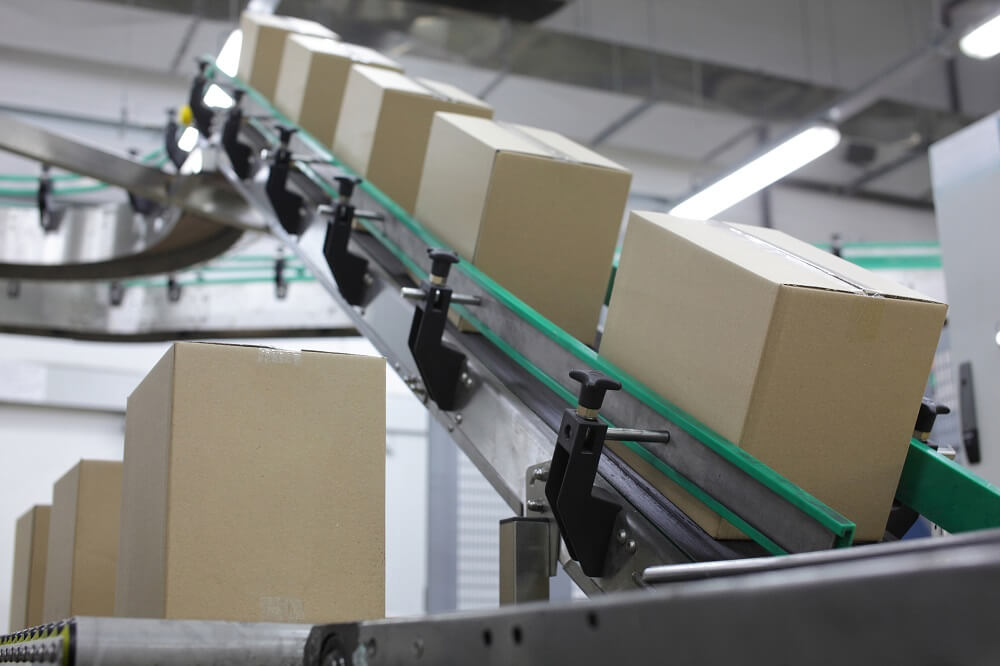
The switch to automation rocked the auto industry decades ago. Now, manufacturing and distribution companies in other industries are considering a move toward more automated facilities. Of course, automation brings one major concern: while new technology can help deliver products more affordably and efficiently, it also leads to cutting jobs. The switch to automation brings another challenge as well — it completely changes the way companies build and use real estate, as automated equipment has different needs than human employees do.
Manufacturers and distributors need to know how a move toward automation changes their real estate strategy. As industrial practice lead at Cresa, I’ve seen how automation has affected real estate plans for manufacturers and distributors. Here’s my advice if your company is facing big decisions about automation.
Understand Your Return on Investment
Advances in automated equipment in manufacturing and distribution have made for some amazing capabilities, but it’s important for companies to understand the return on investment if they purchase automated equipment. Automation can bring more accuracy and efficiency, but organizations need to put in the work to determine whether a purchase is right for them at that time.
Dig deep into the costs of your manpower for every task and carefully analyze equipment manufacturers’ claims against your own numbers. You’re the only one who will understand how each process is performed today, and how automated equipment will change the outcomes.
Time Your Equipment Purchases Carefully
The question of automation often comes up when companies are approaching the end of their lease or are thinking about moving. Because automating equipment is a significant capital investment and takes up floor space, there’s a natural curiosity about it that arises when companies are looking at their real estate portfolio. That’s when leaders start asking the question, “can we automate this process?”
In addition, automation equipment requires very specific building requirements. Many companies don’t have facilities that will easily accommodate that equipment, so they have to wait until they move to automate. You can’t just add specialized automation equipment to any building. Some systems require ceilings of a certain height, a specialized electric capacity, enhanced floor loading, and additional heating or cooling. It’s important to think about how large pieces of equipment will get in and out of the building.
Look for Automation-Ready Properties
As automation becomes more common, its role in the real estate market will grow. While the addition of automation has increased, we’ll continue to see more automation over the next ten years. That means more buildings with conveyor belts, shrink-wrappers and carriers, and new distributor spaces for those machines.
Do your homework before you dive into automation, and consider the impact on your current space and long-term real estate strategy.